First-of-a-kind program infuses Big Data, advanced analytics and modeling to merge mechanics, field knowledge and diverse data sources to increase operational performance in mine production
SAN JOSE, Calif., and Queensland, Australia – 20 Feb 2014: IBM today announced a new collaboration with Thiess, one of the world’s largest contract miners, to use Big Data to improve machine availability and operational productivity utilizing predictive analytics and modeling technologies. This initial collaboration focuses on Thiess’ Mining haul trucks and excavators, and will help unify asset management and business operations.
Unlike traditionally data-intensive industries such as banking or telecommunications, which rely on advanced information technology (IT) to drive operational performance, asset-intensive industries such as mining, have typically not invested as much operationally in IT systems.
Today, many organizations in natural resource industries rely heavily on either a ‘fix-it-when it-breaks’ approach or time-based scheduled maintenance techniques. These methods often result in unnecessary downtime, premature component replacements, extra expense and lost production. They also do not explicitly factor in an individual piece of equipment’s actual condition and performance capability.
However, this trend is changing, as companies realize how IT can help them extract liquid, rocks and insights out of the ground. The increased deployment of machine and environmental sensors combined with new data collection methods is enabling the development of predictive machine maintenance analytics which can help increase equipment availability, lower production costs and provide greater operational flexibility.
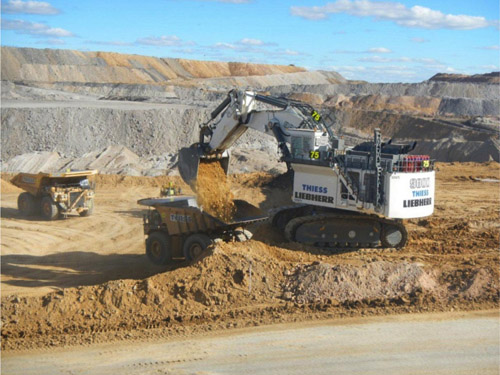
IBM Equipment Condition Monitoring for Natural Resources. IBM developed an intelligent condition monitoring technology using the most comprehensive data set ever assembled in this domain. This system proactively presents decision support information to drive actions that reduce downtime, increase fleet productivity, and minimize maintenance costs. (Image credit: IBM Research)
The IBM Research and Thiess collaboration has been integrating current and historical machine sensor data, along with maintenance and repair, operational, and environmental data to use as a basis for data-driven operational optimization. Factors such as repair and inspection history, payload size, sensor-based component alerts, operator variability, weather, and ground conditions are being used to construct models which assess and predict the life of discrete components and the overall health of a piece of equipment. This information will enable decision makers to co-optimize maintenance and production decisions, resulting in better operational performance.
“Analytics and modeling can offer great opportunities to improve our business, but we need to integrate them with our current processes in order to have a real bottom-line impact. Working with IBM to build a platform that feeds the models with the data we collect and then presents decision support information to our team in the field will allow us increase machine reliability, lower energy costs and emissions, and improve the overall efficiency and effectiveness of our business,” said Michael Wright, Executive General Manager Australian Mining, Thiess.
Early detection of even minor anomaly and malfunction patterns can be used to predict the likelihood of component failures and other areas of risk. This will dramatically increase the uptime of the equipment and improve Thiess’ ability to manage the full life of discrete components, overall machine health and the deployment of limited maintenance resources.
“Natural resource industries are facing a perfect storm of demand growth, scarcity and rising costs that threaten their ability to deliver materials, fuel, and food to the world,” said Matthew Denesuk, Manager of Smarter Planet Modeling and Analytics, IBM Research. “By combining knowledge of the physical health of the equipment with information about how it needs to be used, we are able to know when something is going to go wrong and what can be done to fix the root problem before that occurs.”
Developing a unified predictive equipment and operational management system requires finding common connection between physical and computer scientists, who often operate with different skill sets and goals. The models used in this project bring together the physical and digital worlds by supplementing data-driven modeling that computer scientists tend to employ with information from engineers who have first-hand expertise about the mechanics of the equipment.
Predictive machine management differs from traditional machine management in several ways. First, it bases decisions about a machine’s maintenance and operation on the actual condition or health at that given time. Second, it has the ability to predict the health of a given machine far enough in the future to enable decision makers to execute correct actions such as adjusting production plans or ordering spare parts.
For example, in one mining scenario, several haul trucks that move coal may be reported to need maintenance, while at the same time a substantial order of product is due for delivery in 11 days. The predictive machine management system will be able to look at a variety of options for addressing this problem, and provide a decision maker with a model-based prediction that if the trucks are loaded no more than 85% of normal capacity and driven at no more than 80% of normal speed, the failure probability over the next 11 days would be minimal. This allows companies to avoid badly-timed and costly downtime at the sacrifice of only a minor, temporary decrease in throughput.
*Source: IBM