By Shawn Clayton
When a company can print an entire home in less than 24 hours for under $10,000, it’s somewhat surprising that it’s not front-page news for several days in a row. However, most people haven’t even heard of start-up companies like Apis Cor and New Story. These organizations are making tremendous strides to close a gap and provide functioning homes to the many people who need them with the help of 3D printing. While still in its infancy, additive manufacturing may soon be poised to revolutionize an industry that, in many ways, could desperately use a shake-up.
Efficiency at its Finest
When a building can be both built and furnished with a 3D printer, it opens up opportunities that we might never have considered even 10 years ago. 3D printing offers conservation benefits that can’t be found in traditional methods, making it one of the fastest-growing sustainable building technologies beyond simply using sustainable materials. For example, concrete components of a building are crafted rather than formed, a process that allows the structure to be hollow. So a 3D printed building will use less concrete without threatening the structural integrity of the building. Plus, this new technique eliminates the need for forging and molding — time-consuming activities that bump up the price of the home and delay production.
Current Events
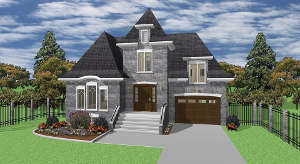
Image courtesy of Pixabay
Recently, a non-profit organization in Silicon Valley called New Story teamed up with Icon, a company focused on developing new technology in the construction industry. The idea behind their collaboration was to build a printer that could manufacture a home for just $4,000. Right now, the conversation surrounding 3D printing is part wonder and part humanitarian.
An architect might marvel over the flexibility they have when it comes to design, but a social worker in a developing nation may see a way to get their clients out of their current home and into something far more livable. It may not be the go-to method just yet, but the advantages of 3D printing are slowly starting to spread.
Cutting Costs
It’s not clear exactly how 3D printing will look in the future. Some companies claim that they can cut down on up to half the cost of a normal home. As more competition takes the stage, many hope that it will become the answer to impoverished people who need safe housing. The reduced need for materials would give the green movement a huge boost, and the models 3D printing provides should translate to fewer mistakes or delays. Essentially, the inexpensive models that 3D printing can produce will give leaders an easier way to spot potential problems before they have a chance to interfere with the mission of the project.
A More Transparent Process
Those who choose to use this technology will have a way to give their clients more information when it comes to the building process. Too often, clients and construction companies clash because a client can’t even imagine what it’s like to keep track of the countless moving parts on the job. A company leader may lack the communication tools (or the time) to thoroughly explain the scope of the job. But with 3D models and printing, a client has a way to visually see what’s happening and why. It lets them express their own needs before building even starts rather than mid-way into construction.
Potential Barriers to Adoption
Even though the actual cost for the homes is rather low, the cost of building the actual printer is exceptionally high. As simplistic as it might look to an outsider, those in the industry know that printers have limitations when it comes to where they can be run and how the materials can be used. A printer that creates a floor or a wall may do so in an offsite facility before it needs to be transferred to the site and then manually assembled with the rest of the home. Construction companies may be better off working with smaller items or special requests to the home than they would be to rely on it for constructing the full home — for now anyway.
Still a Way to Go
As technology launches us into the future, home inspectors may struggle to keep up if new technology isn’t taken into account with training and education. While many of the homes that have already been made have been declared ‘fully up to code’, those in quality control are likely to struggle with declaring a building ‘safe’ when they don’t understand how it was made. Despite all of this, though, engineers and architects are closely following the industry as it unfolds so they can be at the forefront of the technology if and when it becomes mainstream.
There are plenty of reasons to be excited about what 3D printing and other emerging home technologies can do for the construction industry. It may no longer be a given that people need to wait months to find a home of their own for a price they can afford. It can open up new career opportunities for those who choose to embrace the revolution while cutting down on the number of resources a completed home requires. There is still some work that needs to be done before this technique becomes a truly viable alternative to traditional building, but it’s certainly something to keep an eye on.